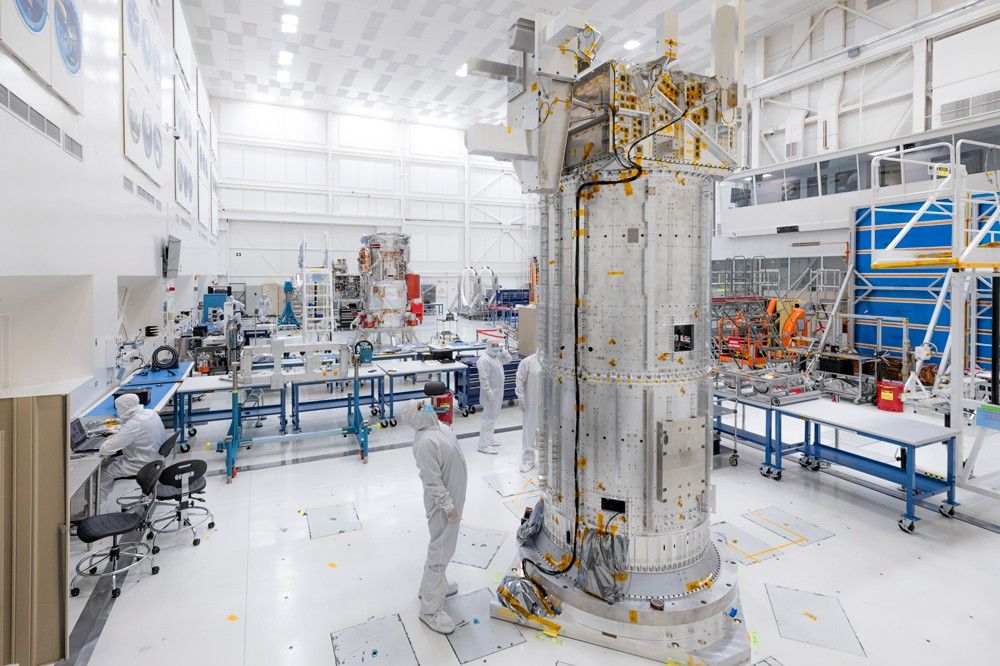
To ensure NASA’s Europa Clipper can withstand the physical stresses of launch and hundreds of millions of miles of space travel, an engineering team is testing a full-size copy of the spacecraft’s central structure at NASA’s Jet Propulsion Laboratory (JPL), in southern California. The duplicate spacecraft is called the developmental test model.
“Structurally it’s identical,” said Benjamin Marti, a mechanical engineer at JPL and Europa Clipper’s static test lead, referring to the test model that replicates the spacecraft’s central stucture. “It’s built to the same drawings and assembled from the same materials with the same fasteners as the flight model.”
The test model replicates Europa Clipper’s propulsion module and electronics vault. While the test model will never go to space, testing these components is essential because the propulsion module and electronics vault form the load-bearing central core of the spacecraft. The vault will shield the spacecraft’s vulnerable hardware from high-energy particles trapped in Jupiter’s magnetic field, while the propulsion module is an aluminum cylinder about 10 feet (3 meters) tall and 5 feet (1.5 meters) in diameter. The flight version of the propulsion module will include electronics, radios, thermal loop tubing, cabling, and the propulsion system.
During a May 2022 static test, the team ran 12 powerful hydraulic cylinders at the same time to simulate the forces Europa Clipper will experience during launch – the most kinetically intense segment of the spacecraft’s journey. In static testing, force is applied gradually and steadily to the test model, as opposed to dynamic testing, which applies sudden motion, such as intense shaking.
The test model was installed in a static test tower at JPL where the hydraulic cylinders similar to those on bulldozers and other construction equipment pushed and pulled on it to exert enormous forces. “We can apply loads of about 40,000 pounds with each hydraulic cylinder,” Marti said. Though previous spacecraft have been tested in the same static test tower at JPL, Europa Clipper’s test model broke records as the largest item to be tested in the tower.
Like countless other engineers at JPL, Marti’s career has taken a winding path, and he seems to relish big changes to his work and the settings where he performs it. Several years ago, Marti was a civilian test engineer for Naval Air Systems Command. “I worked at a rocket sled track,” Marti said. “A big part of my job there was testing parachutes and other decelerators for JPL.”
Prior to putting Europa Clipper’s test model under pressure, Marti had a stress test of his own. “My team performed the final set of operations on the Mars 2020 Perseverance spacecraft: installing the radioactive power source, filling and activating the thermal control system, and finally closing the door on the spacecraft,” he said.
Marti considers July 14 through July 30 of 2020 – the final two weeks leading to launch – to be the most stressful period of his life, but also the most rewarding. Roughly seven months later, in February of 2021, the mission’s Perseverance rover and Ingenuity helicopter landed on the Martian surface, where they have been exploring Jezero Crater ever since.
Much of Marti’s work for Mars 2020 was in a clean room. In those carefully controlled environments, personnel must wear a white, full-body covering known as a “bunny suit” and must be ever vigilant to avoid damaging or contaminating spacecraft, in addition to doing the task they are in the room to perform.
When compared to a rocket sled roaring down a test track at hundreds of miles per hour, or to working hectically in a clean room, Marti’s present work might seem relatively quiet, slower-paced, and meticulous. But he found working with the Europa Clipper test model exciting and fun for other reasons. “It’s awesome – this spacecraft is a monster,” Marti said. “It’s large and heavy, so we were pushing the height of our cranes and the strength of our floors. Europa Clipper’s assembly and test flow is forcing us to get smarter so we can continue working with our existing infrastructure.”
Two teams worked in parallel for about a year and a half to prepare for testing Europa Clipper’s test model. One team focused on preparing the test model while the other team evaluated the test tower. Though the spacecraft is the thing being tested, engineers needed to know that they wouldn’t break the building in the process. The team even scanned the test tower to create a computer model so they could evaluate in detail whether the building could handle the testing program.
To design the static tests, analysts calculated the peak and cumulative stresses Europa Clipper will experience during its journey. From those calculations, the team developed five scenarios called “load cases” or “pull cases” in which hydraulic cylinders pushed and pulled on the test model in specific ways to simulate flight stresses. However, 60-plus years of spaceflight history have taught engineers that “adequate” doesn’t always do the trick. So the team designed the tests to apply 20 percent more force to the test model than Europa Clipper is predicted to experience on its journey.
For each of the static tests, the team attached “mass models” to Europa Clipper’s clone to represent absent components, such as solar arrays or science instruments. Between 60 and 80 strain gauges were affixed to carefully-chosen locations on the test model and they sent data to nearby computers, which ran on code modified from the static tests for the Mars 2020 Perseverance rover.
While the hydraulics pushed and pulled, the test team watched the computer monitors and compared the real-time strain data to predictions based on calculations beforehand. If the strains exceeded predictions, the team paused the test to analyze the discrepancy. The static tests took about three months before wrapping up in June.
Europa Clipper’s test model has now been moved into High Bay 1 in JPL’s Spacecraft Assembly Facility, where it is being configured directly next Europa Clipper’s flight model’s main body and avionics module — the spacecraft components the test model are designed to replicate.
While engineers are currently assembling the flight model’s main body and avionics module, the test model will be undergoing modal testing. During modal testing, the test model will be excited with shakers and the spacecraft’s dynamic response measured. The test model was moved to High Bay 1 because JPL’s largest “seismic mass” lives in the corner of the high bay. The seismic mass is a 1.16 million pound concrete block set into the floor of the facility. During modal testing, engineers will bolt the test model to the seismic mass. The modal test will help verify the team’s analytical spacecraft models, helping engineers ensure that the Europa Clipper spacecraft will handle launch.